Quick Summary
- DFMA reduces manufacturing costs by up to 50% through part count optimization, standardization, and automation-ready design.
- It enhances supply chain resilience by minimizing dependencies on single suppliers and simplifying logistics and assembly processes.
- KEK Design empowers companies to adopt DFMA as a strategic tool for reshoring, faster time-to-market, and long-term competitive advantage.
In today’s global market, manufacturers face relentless supply chain disruptions and mounting competitive pressures. From geopolitical tensions to material shortages and logistical challenges, operational uncertainty is the new norm. At KEK, we encourage companies to turn to Design for Manufacturing and Assembly (DFMA).
DFMA isn’t just an engineering tactic; it’s a strategic methodology that embeds efficiency, manufacturing risk reduction, and cost control directly into product design. By simplifying product architecture, reducing part counts, and standardizing components, DFMA helps businesses cut total manufacturing costs by up to 50% while boosting supply chain resilience.
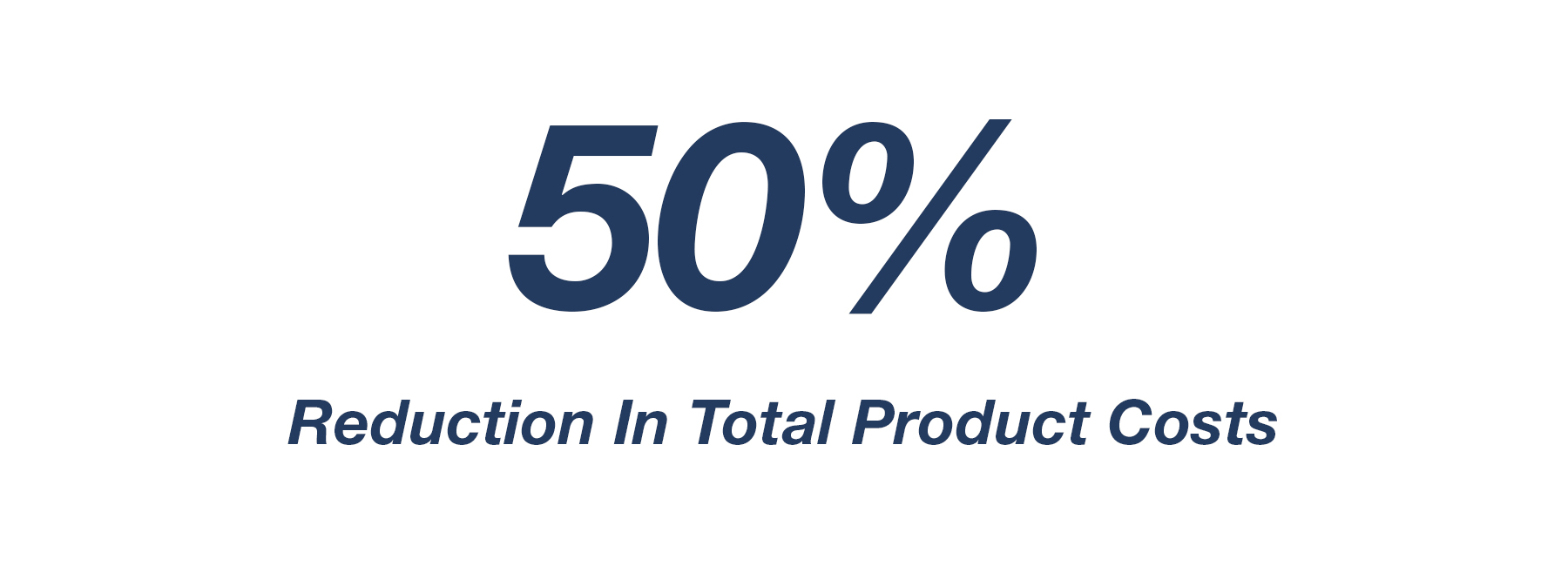
Why DFMA is Essential for Modern Manufacturing
Traditional manufacturing models often treat design, production, and supply chain management as separate silos, a costly mistake in today’s volatile environment. DFMA bridges these gaps by aligning design choices with manufacturing realities from day one. The result? Faster time-to-market, lower costs, and products inherently designed to withstand supply chain disruptions. This is where understanding DFA vs DFM becomes crucial, integrating both under the DFMA umbrella ensures complete design efficiency.
Build Supply Chain Resilience Through Smarter Design
Incorporating DFMA principles proactively reduces vulnerabilities. Whether it’s avoiding delays due to component shortages or navigating geopolitical instability, DFMA gives manufacturers the flexibility to adapt quickly. For companies exploring reshoring or regionalizing production, DFMA can offset higher labor costs by enabling design automation and reducing manual assembly.
For example, how to reduce part count in product design becomes a critical question early in the development cycle. Optimizing for minimal parts leads to simplified modular product design, easier maintenance, and faster builds, all key aspects of supply chain-friendly product development.
This strategic approach transforms DFMA from a cost-saving tool into a core element of supply chain risk management and competitive positioning.
Unlock Competitive Advantage with DFMA
In high-cost environments, DFMA levels the playing field. By reducing labor content and enabling automated assembly, companies can maintain profitability without chasing low-wage regions. Additionally, DFMA aligns seamlessly with advanced manufacturing technologies like 3D printing and engineering prototyping, driving innovation alongside efficiency.
Industries from automotive to construction are already leveraging examples of DFMA in real-world manufacturing to streamline operations and enhance agility. Is your business ready to join them?
Download Unlocking Design for Manufacturing and Assembly
Gain in-depth insights into how DFMA can revolutionize your product development and manufacturing processes. This comprehensive guide covers:
- Design in an Era of Uncertainty
- Deconstructing DFMA: Principles, Methodology, and Goals
- Forging Resilience in Volatile Supply Chains
- Resurgence of Domestic Manufacturing Competitiveness
- Recommendations to Implement DFMA from KEK Design
As the leading product design firm in Rochester NY, KEK Design brings over 50 years of experience helping clients cut costs, accelerate timelines, and reduce risks. We are proud to be recognized as trusted manufacturing consultants delivering high-impact DFMA services. Don’t let supply chain volatility dictate your success. Download the eBook today and discover how to embed resilience, efficiency, and flexibility into every product you design.